一:控制设备及设计范围
(1)主要控制对象为:
框槽配料系统:振筛、称斗、称重、输料皮带、除尘阀门
Ø
炉顶上料系统:料车卷扬、探尺、布料器、溜槽倾动、料流阀、炉顶液压阀门、炉顶电动阀门、冷风放散阀。
Ø
热风炉系统:液压阀门、助燃风阀门、煤气和助燃风流量调节阀
Ø
布袋除尘系统:煤气总管阀门、净煤气荒煤气支管阀门、布袋放散阀、布袋卸灰阀、仓壁振动器、布袋卸灰给料机、布袋系统出灰拉链机、布袋系统出灰斗提机、灰罐卸灰阀及加湿器、布袋吹扫脉冲阀。
Ø
高炉本体及水系统仪表
(2)高炉自动化系统设计范围:
框槽配料系统低压配电、自动控制plc系统配置及软件、称量仪表监测系统Ø
Ø
炉顶上料系统低压配电、自动控制plc系统配置及软件
热风炉系统低压配电、自动控制plc系统配置及软件、仪表检测系统Ø
Ø
布袋除尘系统低压配电、自动控制plc系统配置及软件、仪表检测系统
Ø
高炉本体仪表及水泵房仪表检测系统
二:高炉自动化系统设计概述:
高炉电气自动化系统主要是通过PLC自动化控制系统,完成高炉生产的主体设备或系统的自动生产任务,以及生产设备以及生产现场的监控任务。同时为了调试或是检修等目的辅以其它的控制方式。
1:整体控制方案简介
设计有现场就地控制方式和PLC自动控制方式两种。同时对个别需要紧急操作的设备或群组设操作台集中手动操作。
1.1:现场就地方式:
对于主要的生产设备,在设备现场设置就地箱,主要用来设备的调试和后期的维修作用。为简化线路,减少因就地箱带来的后期维修,设计原则以简单为主,兼顾实用性。
考虑到全自动系统只有在某个独立的系统(如布袋系统、热风炉系统、高架系统、配料系统、上料系统)安装完毕后方具备调试条件的要求,从而延后了整体的调试周期。而采用就地方式完全可以单机调试,从而争取了调试时间,为系统的早日投产创造更好的基础。同时,现场控制方式因其直观和方便性,更适合后期的设备维修还检修,可以有效的降低维修时间,提高设备的运转率,能为高炉的高效生产奠定良好的基础。
针对现场就地箱的设计目的,在设计中采用最简电路和原理,采用最少器件的原则,从而可以有效的降低因就地箱带来的后期维护。
另外,设计中对不必进行集中控制的生产辅助设备仅采用就地控制。比如粉料仓的卸灰阀(或闸门)、加湿器等设备。
1.2:PLC自动控制方式:
此方式为生产方式,现场设备根据PLC内部逻辑程序的控制自动完成生产工作。操作人员可以在电脑显示屏上对生产进行控制、设置以及观察设备的运行状态。
1.3:操作台集中手动操作:
对生产设备中如:布袋方散阀、布袋系统总管阀门、重力除尘放散阀、热风炉助燃风总管管道阀门、炉顶放散阀设计成操作台集中手动操作。一方面以上设备或是不需要经常的操作,或是需要脱离PLC后依然能够收到工长的控制。
2:自动化系统的网络结构及硬件配置
2.1:系统硬件选型及方案
本着先进、可靠的原则,进行各种方案分析评价、对比,决定选用西门子自动化平台。整个系统共分3个子系统,6个上位监控站,3套可编程控制器。
考虑实际控制性能和综合成本,为获得更好的性价比,系统采用ET200M分布式控制系统。设计采用3台S7-414/412系统作为主站,通过ET200M外挂现场控制从站,从站采用S7300系统模块。各主站统一设置在高炉主控室内,每个系统中各个从站分别放置在相应的子系统控制室。主从站之间采用网线连接,从而减少了布线故障和干扰。同时输入输出模块预留10~20冗余。
编程软件采用SETP7,为控制系统编程提供专门的多语言开发环境。具有生成标准导出功能块库或DFB库能力的编程器,它们能够在应用程序内重复调用。(自动化系统配置依系统大小进行相应调整)
监控软件采用扩展性、灵活性极强的WIN
CC6.0系统。实现对生产过程的全面监控,并且可以对重要参数形成历史记录,以报表或曲线的形式显示给操作人员。
2.2:系统硬件配置:
高炉计算机控制系统所有PLC设备选用西门子自动化平台,每套PLC系统通过插在主底板上TCP/IP
Ethernet模块连接在100M快速局域网上;上位监控机采用集中式设计,采用快速100M以太网。上位监视系统由5操作站、1台工程师站组成以太网。
工程师站:该站设置于高炉主控室,内含高炉系统全部的控制程序和监控画面,可完成对所有设备的控制。
控制站:现场控制站计算机系统选用西门子的PLC产品。根据高炉生产系统的特点和作用以及PLC硬件本身的容量、控制室的分布,高炉自动化系统设计由三各系统构成:热风布袋系统、高炉仪表监控系统、高炉上料系统。其中每个系统设两到三台上位监控微机;采用一个s7400的CPU,系统中的每个子系统采用ET200M分布式远程I/O结构与s7400
CPU相连接。
2.3:各子系统硬件配置
2.3.1:热风布袋系统
主要完成热风炉、布袋除尘系统的自动控制。监控上位机两台,PLC采用一台s7412
CPU,下设五个ET200M分布式远程I/O。
其中热风炉设两个ET200M分布式远程I/O,分别完成热风炉烧炉、闷炉、送风电气自动控制、热风炉仪表自动控制。
布袋净化系统设三个ET200M分布式远程I/O,分别完成布袋煤气净化电气自动化控制、布袋脉冲除尘及下灰电气自动化控制、布袋仪表自动化系统。
2.3.2:高炉仪表监控系统
主要完成高炉个热工仪表点的监测,如炉内压力、温度、循环水压力温度、氮气压力流量、热风压力流量,以及炉顶压力的控制等工作。监控上位机两台(其中一台兼作工程师站),PLC采用一台s7412
CPU,下设两个ET200M分布式远程I/O。
2.3.3:高炉上料系统
主要完成高架供料、框槽配料、炉顶上料的自动化控制。监控上位机三台(根据高架是否采用自动控制选择),PLC采用一台s7414
CPU,下设六个ET200M分布式远程I/O。
其中高架供料系统设两个ET200M分布式远程I/O,分别完成高架供料的料仓补料的自动控制(根据用户选用)、高架上料除尘系统阀门(根据用户选用)自动控制。
框槽设两个ET200M分布式远程I/O,控制完成框槽振料自动控制、框槽配料和运料自动控制、除尘阀门自动控制。
炉顶上料系统设两个ET200M分布式远程I/O,完成料车上料控制及保护、探尺料面探测控制、布料控制(料流阀、倾动、旋转布料器)等工作。
2.4:网络结构
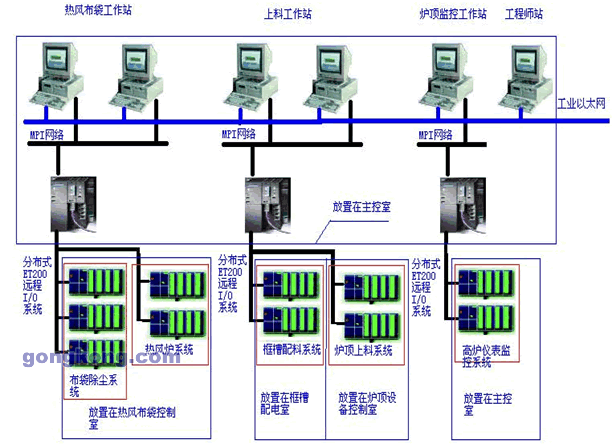
3:计算机系统功能
3.1计算机控制功能
3.1.1:高炉本体控制功能
实现数据采集、炉顶压力减压阀组调节阀控制、混风温度调节控制、炉顶料钟自动控制、氧气总管流量调节控制、画面显示操作、实时趋势、历史趋势、报警记录和报表打印等功能。
3.1.2:槽下控制功能
实现对矿石、球团、烧结、焦炭等入炉原料的自动称量,并完成称量误差的自动补偿;实现槽下14个仓、14个称量斗、2条成品带、2条碎矿皮带、14台振动筛的自动控制,以及自动备料和放料。可对设备的运行进行手/自动切换和强制动作,并进行料单更改;对装料超时、放料超时等情况进行报警。
3.1.3:热风炉控制功能
主要对三个热风炉的监视、连锁控制。实现热风炉助燃风、煤气、烟气、冷风、热风等阀门的动作,实现热风炉送风转燃烧、燃烧转送风的控制过程。热风炉有三种工作制:两烧一送,两送一烧,一烧一送,具有全自动/半自动/手动控制燃烧与换炉操作。
3.1.4:煤气净化系统
系统控制煤气净化设备的单机、连锁控制功能,实现生产的监视、设备的控制、工艺参数的稳定功能。
3.1.5:炉顶卷扬控制
主卷扬运行制度:主卷扬采用西门子
PLC,料车到料坑底发出到位信号,开启料斗闸门,料空且闸门管好后,发出上行信号,将料装入受料斗。
碎焦卷扬控制:振筛工作停止,启动碎焦卷扬,如果解除联锁,也可手动控制。
3.2:画面监控
绘制多幅工艺流程画面、设备启停画面、工艺参数画面、阀门操作画面、设备方位图、报警画面、报警纪录、历史纪录、实时趋势以及历史趋势画面。使操作人员可以通过画面监视整个生产过程,启停设备、监视参数、调节阀门,观察趋势,查询历史纪录。
3.3:
历史趋势
对一些重要参数,如热风温度、热风压力、冷风流量、冷风压力、炉顶压力、左右探尺等,我们对其进行历史数据存储,形成历史趋势,可以随时进行查看。
3.4:参考画面(以下画面仅供参考,具体画面以实际设计为准)
图一:热风炉工艺总图:
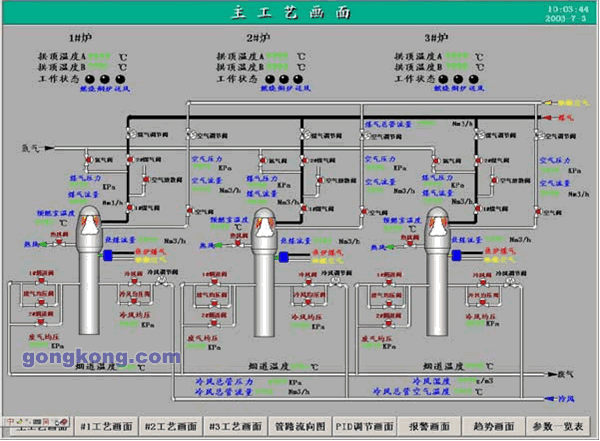
图二:高炉本体监控画面
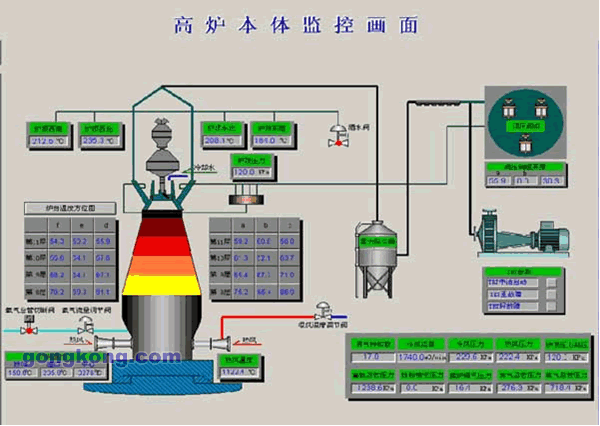
图三:高炉炉顶监控画面
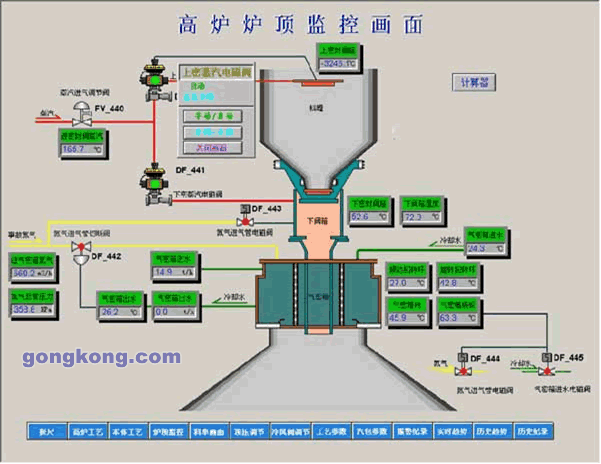
图四:高炉工艺流程图

图五:高炉管道流向图
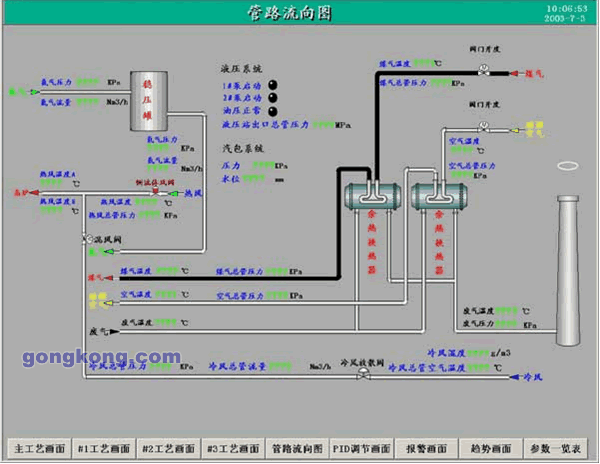
图六:高炉框槽配料流程图
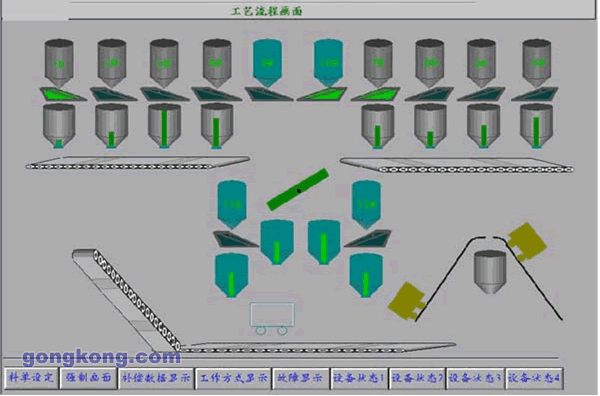
图七:高炉料单画面
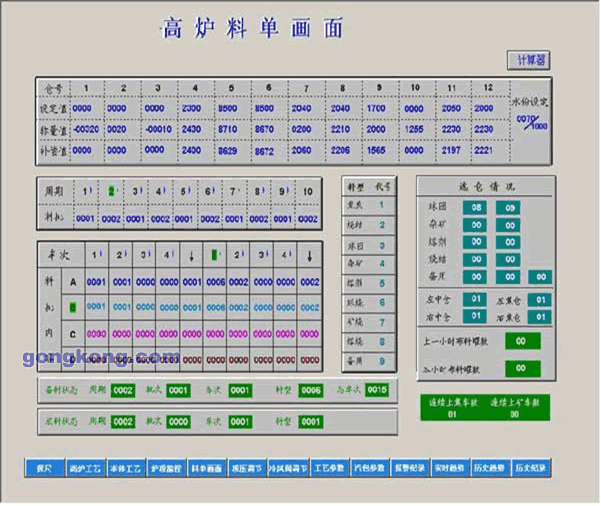
图八:高炉框槽设备状态
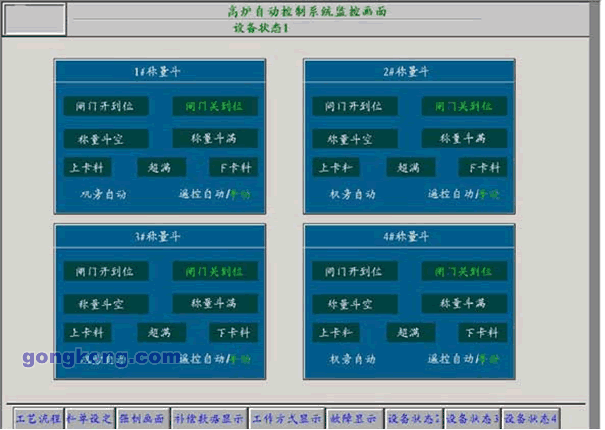
图九:高炉冷风调节
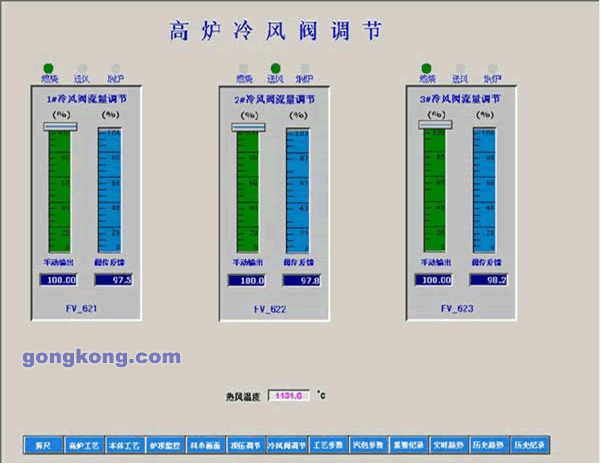
图十:高炉炉顶压力调节
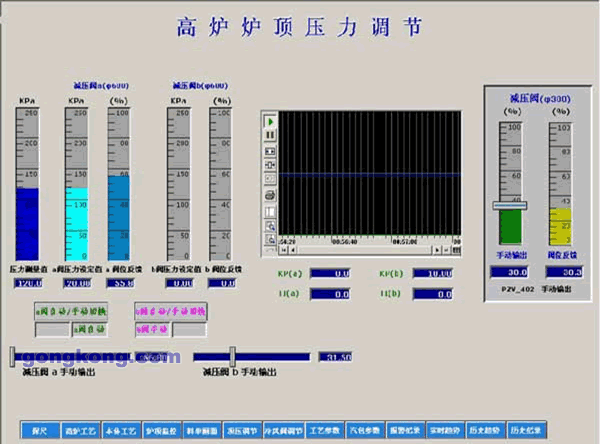
图十一:高炉本体工艺参数图
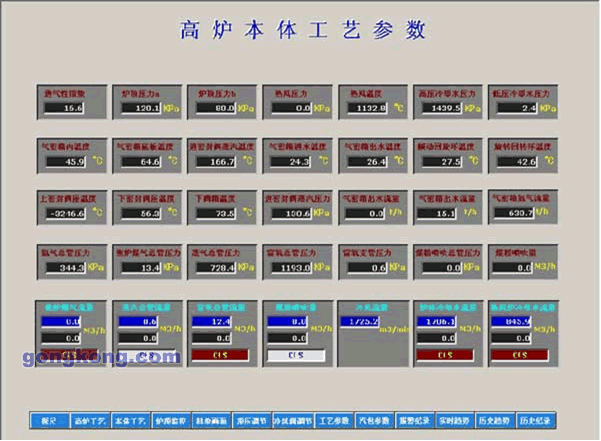
图十二:高炉实时曲线图
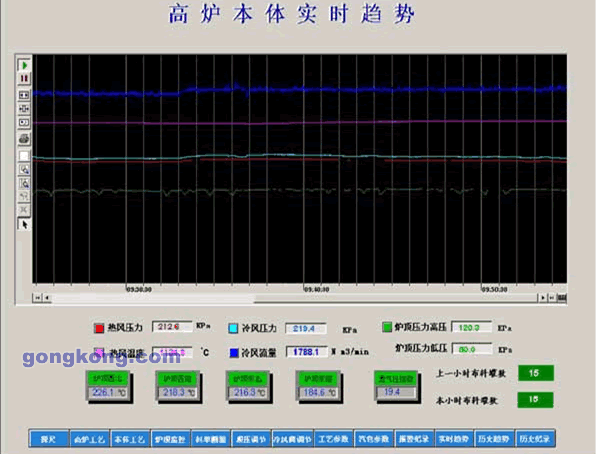
图十三:高炉历史曲线图
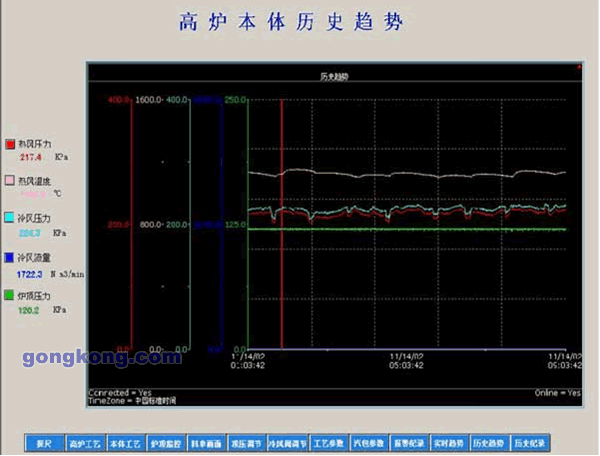
图十四:报警纪录
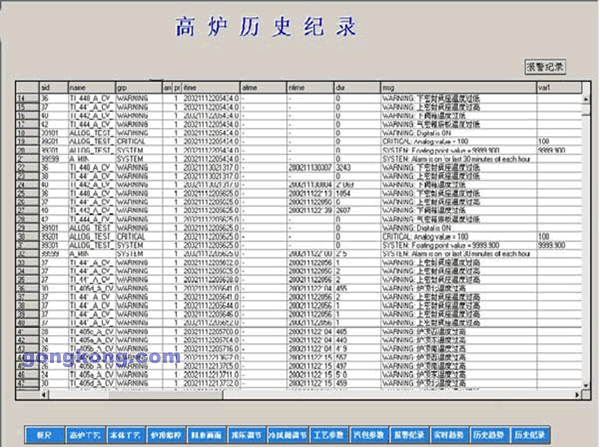
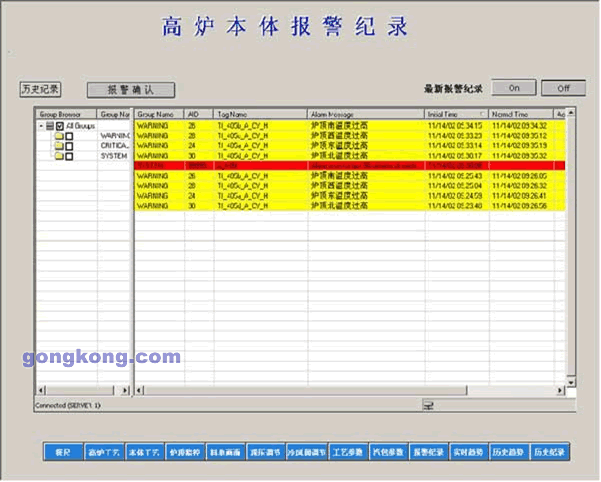
4:电气拖动控制系统设计
4.1:系统配电设计
4.1.1配电室设计:
系统设计以下配电室:炉顶上料配电室、热风布袋配电室、框槽及高架配电室(如现场有条件,高架单独设立配电室),各配电室采用单电源方案,如果现场要求,可采用双电源供电。
4.1.2:生产设备配电及拖动控制
针对现场设备的再生产中不同的作用和工作特点,分别采用集中配电控制和现场配电控制两种方式。
4.1.2.1:集中配电方式:
对于直接参与生产任务的设备采用控制室集中配电方式,如高架上料中的皮带、振动筛、分料器;配料中振筛、液压系统、皮带;炉顶上料中的料车卷扬电机、探尺、布料设备;热风炉液压站及助燃风机阀门;布袋除尘系统的管道阀门、卸灰系统设备、重力除尘设备等。
4.1.2.2:现场配电控制方式:
对于非直接生产用设备,如高架粉料仓闸门、配料系统粉料仓闸门等采用采用现场配电控制方式。同时对于移动设备,如高架布料小车亦采用此方式。
4.1.2.3其他方式:
同时对于相对独立的设备群,采用就近集中配电控制,如高架上料系统的地下料仓中的设备。如果现场不具备集中配电室空间,则改为单体现场配电控制方式,并辅以电源柜统一供电。进而减少安装的电线电缆的投入和工期投入。
4.1.3:供配电柜体及箱体选型设计
配电室配电柜采用GGD2型交流低压配电柜。GGD2型交流低压配电柜符合IEC439《低压成套开关设备和控制设备》、GB7251《低压成套开关设备》等标准。适用于发电厂、变电站、工矿企业等电力用户的交流50HZ、额定工作电压380V、额定工作电流3150A的配电系统,作为动力配电和控制用途。
现场操作箱或配电箱采用双层门(外层为有机玻璃门)防尘壁挂式结构,充分保证了防尘及防护的要求。
现场临时配电采用XL21配电柜作为临时现场配电系统,根据现场设备的布局确定具体的数量。
4.2:电气控制设计
系统电气控制设计遵循以下原则:
A:以PLC控制为主,其他控制为辅的原则,兼顾最简电路设计和最少现场走线设计
B:对PLC输入输出采用电气隔离以减少对PLC的损坏
C:合理排布端子,减少布线干扰
具体做法如下:
对以自动控制为唯一生产控制方式而又不需要长时间调试的设备,如配料系统中的挣动筛、布袋系统的仓壁震动器等设备采用手动下点动控制,从而简化了电路;而位置阀门类设备采用自锁式转换开关控制方式。
取消就地操作箱上运行状态指示,仅保留位置状态指示。
根据区域分布合并现场控制箱,或是采用功能设备组方式设计就地箱,而不再采用每一个设备一个就地箱。
对于带有现场位置检测的设备,采用位置信号现场就地箱中转方式或是将为之开关转换继电器直接放在现场就地箱,一方面可以减少现场到控制柜远程布线,同时便于维修。
对PLC输出,均进行继电器隔离;而对于远程(现场到PLC)输入,也采用继电器隔离。从而防止不同电压对PLC的损坏。
根据配电柜布线走向(柜间、柜外)和电压等级,对出线端子进行合理排布,尽量避免柜间走线和柜外走线的交叉缠绕、避免不同电压等级的电线电缆交叉缠绕。
4.2:电气拖动设计
针对设备容量和负载特性,对现场设备分别采用电磁拖动、软起加电磁拖动、变频拖动、伺服拖动几种形式。其中对于小容量电机如振动筛、阀门、给料机、小负荷皮带机等采用电磁拖动;对于大容量又不需要调速的(大于75kw皮带电机)负载采用软起加电磁拖动;对于料车卷扬、旋转布料器等调速设备采用交流变频器拖动;对于探尺卷扬采用支流调速器拖动;对于伺服电机采用伺服控制器拖动。启动对于交流变频调速中的料车卷扬、旋转布料器以及伺服电机这些重要设备设计备用系统,以提高设备的运转率和降低生产事故。
5:器件选型
器件选型本着实用合理的原则,以及考虑备品备件和器件应用的普遍性、应用技术的成熟性来选配,同时对于现场仪表一次元件在兼顾性价比的基础上,更注重是否安装的便捷,是否有利于缩短施工工期。
本着上述原则,对系统器件作如下选型:
5.1电气器件选型
其中低压一次元件采用LG或施耐德产品、对于交流变频器设计采用施耐德ATV71系列产品、直流调速器采用西门子6RA70系列产品、伺服控制器采用山羊Q系列产品、中间继电器采用欧姆龙产品。
其中LG产品,该产品和施耐德等品牌具有相当的性价比,同时因其进入中国市场较晚,较其他进口品牌相比具有更好的保真,更主要的是该公司每只产品在投放市场前均经过模拟老化调校,从而有更好的质量保证,从而成为我公司系统的优先选型器件。
施耐德变频器在国内特别是冶金行业应用非常普遍,应用技术相当成熟。同时大容量的ATV71系列变频器率先采用整机产品,这样大大减少了安装时的一次布线,具有根好的电磁兼容性,可以有效的降低电磁干扰。
5.2仪表选型
在我公司系统设计中,仪表主要选择以下型号:
流量计:采用北京衡安特公司生产的弯管流量计和超声波流量计。以上两种流量计与其他计量方式相比较,在保证相同计量精度的同时更具备安装方便,能大幅缩短施工工期的特点,因此成为首选产品。
压力变:选用E+H或是EJA产品
称重传感器:选用北京恒信天正产品
称重便送器:采用秦皇岛诺华电子716系列仪表或是北京恒信天正HT9901系列仪表。以上两种仪表在国内相同仪表中具有价格低质量好的特点。其中秦皇岛诺华电子716系列仪表更被上海大和仪表采用,部分型号代替日本原机;而北京恒信天正HT9901系列仪表在唐山冶金行业广泛采用,应用技术成熟,售后服务好。我公司多年长期采用以上系列仪表,具有丰富的调试及应用经验,能更好的为用户提供便捷的服务。
红外成像:采用唐山方大天正电子的FDGWS-1型红外成像设备。
当然以上器件也可由用户指定。
以上是我公司设计的炼钢自动化方案,请贵公司技术人员多多指正,以便于我们设计出更完善更符合现场要求的控制系统。
唐山市金佰方自动化设备有限公司