本文结合SIEMENS
S7-200型PLC的特点以及电厂输煤系统的特殊要求,介绍了PLC在电厂输煤系统中用于联锁控制的程序设计及应用。
可编程逻辑控制器(PLC)是八十年代发展起来的新一代工业控制装置,是自动控制、计算机和通信技术相结合的产物,是一种专门用于工业生产过程控制的现场设备。
由于控制对象的复杂性,使用环境的特殊性和运行的长期连续性,使PLC在设计上有自己明显的特点:可靠性高,适应性广,具有通信功能,编程方便,结构模块化。
在现代集散控制系统中,PLC已经成为一种重要的基本控制单元,在工业控制领域中应用前景极其广泛。在笔者参与开发的某电厂输煤自控系统中,系统要求在远离输煤廊的主厂房控制室里,对两条输煤线的18台设备进行控制,并实时监测设备的运行状态及皮带跑偏的情况。
鉴于电厂输煤系统的重要性,我们采用PLC实现输煤设备的联锁控制以保证其可靠性和特殊性,工业控制计算机则作为上位机与PLC互相配合,共同完成输煤系统的监控功能。本文将主要介绍PLC的控制应用。
1输煤系统控制要求
输煤系统有两条输煤线,包括给煤机、皮带机、振动筛、破碎机等共18台设备,在电厂中有着极为重要的地位,一旦不能正常工作,发电就会受到影响。为了保证生产运行的可靠性,输煤系统采用自动(联锁)、手动(单机)两种控制方式,自动、手动方式由开关进行切换。由于输煤廊环境恶劣,全部操作控制都在主厂房的主控制室里进行,仪表盘上设有各个设备的启、停按钮,还有为PLC提供输入信号的控制开关。输煤设备控制功能由PLC实现,设备状态监测和皮带跑偏监测以及事故纪录功能则由上级工业控制计算机完成。
为了保证输煤系统的正常、可靠运行,该系统应满足以下要求:
·
供煤时,各设备的启动、停止必须遵循特定的顺序,即对各设备进行联锁控制;
·各设备启动和停止过程中,要合理设置时间间隔(延时)。启动延时统一设定为12s。停车延时按设备的不同要求而设定,分为10s、20s、30s、40s、60s几种,以保证停车时破碎机为空载状态,各输煤皮带上无剩余煤;
·运行过程中,某一台设备发生故障时,应立即发出报警并自动停车,其前方(指供料方向)设备也立即停车。其后方的设备按一定顺序及延时联锁停车;
·各输煤皮带设有双向跑偏开关,跑偏15度时发出告警信号,跑偏30度时告警并自动停车;
·可在线选择启动备用设备。在特殊情况下可由两条输煤线的有关设备组成交叉供煤方式;
·可在线选择启动备用设备。在特殊情况下可由两条输煤线的有关设备组成交叉供煤方式;
·可显示各机电设备运行状况,并对输煤过程有关情况(报警、自动停机等)做出实时纪录。
2 PLC控制系统设计
2.1 PLC选型
根据输煤系统的自控要求,我们选用了德国SIEMENS
公司最新推出的S7-200型PLC,具有可靠性高、体积小、扩展方便,使用灵活的特点。基本CPU单元选用的是CPU214,性能如下:2048程序存储器;2048数据存储器;14点输入,10点输出;可扩展7个模块;128个定时器;128个计数器;4个硬件中断、1个定时器中断;实时时钟;高速计数器;可利用PPI协议或自由口进行通信;3级密码保护。扩展模块选用EM221,8个输入点;EM223,16个输入点,16个输出点。
2.2
系统关系
系统关系如图1所示。
图1
系统关系
在输煤自控系统中,工业控制计算机作为上位机和输煤控制PLC进行通信,对皮带跑偏信号和设备的运行状态进行实时采样,并在屏幕上显示输煤系统仿真画面,可以直观地察看设备的状态。当皮带跑偏(跑偏15度)时,在屏幕上显示报警画面;当设备发生故障或皮带严重跑偏(跑偏30度)时,在屏幕上显示报警画面并向PLC发送事故停车信号。
输煤控制PLC则根据控制开关的输入信号,执行对应程序块,控制电机实现对应的功能:向上级工业控制计算机发送工作组态信息,接收上级工业控制计算机发送的事故停车信号,实现事故停车处理功能并启动报警设备。二者配合共同实现输煤系统的监测和控制功能。
上级工业控制计算机同时实现对电厂其他系统的监控,由工业控制计算机、输煤系统PLC和其他系统的现场设备(PLC、监控仪表)共同构成分布式系统(DCS)。
2.3
运行模式
根据输煤过程的要求,本系统设计了两种运行模式。在一般情况下,采用并行模式,可根据需要单独选用或同时运行输煤一线和输煤二线。交叉模式是由输煤一线和输煤二线的有关设备组成的,仅在特殊情况下选用。
2.3.1并行模式
并行一线:
联锁开车顺序:10#皮带机→8#皮带机→6#皮带机→2#破碎机→2#振动筛→4#皮带机→2#皮带机→2#(3#)给煤机→4#给煤机。
联锁停车顺序:与开车顺序相反,延时时间按上述要求设定。2#、3#给煤机某中一台备用。
并行二线
联锁开车顺序:9#皮带机→7#皮带机→5#皮带机→1#破碎机→1#振动筛→3#皮带机→1#皮带机→1#给煤机。
联锁停车顺序:与开车顺序相反,延时时间按上述要求设定。
2.3.2
交叉模式
交叉线
联锁开车顺序:9#皮带机→7#皮带机→6#皮带机→2#破碎机→2#振动筛→4#皮带机→2#皮带机→2#(3#)给煤机。
联锁停车顺序:与开车顺序相反,延时时间按上述要求设定。2#、3#给煤机其中一台备用。
2.4 PLC程序设计
针对输煤系统的控制要求以及具体控制方案的实现,设计程序流程如图2所示。
图2
主程序流程
2.4.1
程序说明
·子模块0:初始化子程序。在PLC加电时根据各个开关的位置设立标志位。仅在第一个扫描周期执行。
·子模块1:并行一线联锁启停控制程序。根据启动标志位1实现并行一线的联锁启动、联锁停车,并判断事故停车信号以实现事故停车。
·子模块2:并行二级联锁启停控制程序。根据启动标志位2和实现并行二线的联锁启动、联锁停车,并判断事故停车信号以实现事故停车。
·子模块3:交叉线联锁启停控制程序,根据启动标志位3实现交叉线的联锁启动、联锁停车,并判断事故停车信号以实现事故停车。
·PLC的输出信号控制电机的接触器,启动送高电平,停止送低电平。但是,1#破碎机功率达90kW,2#破碎机功率达110KW,需要降压启动,所以启动时PLC送一个正脉冲,停车时PLC送一个负脉冲。
2.4.2
程序特点
·特殊标志位的使用:使用特殊标志位SM0.1,使得初始化子程序(子模块0)仅在第一个扫描周期执行,而在以后的扫描周期不再执行。这样,个别标志位在PLC加电后不受开关变化的影响。例如,并行模式和交叉模式对应标志位仅在关掉主控开关后才能改变。
·内部标志位的使用:在程序中,利用标志位来表示不同的现场情况和程序状态,增加了程序的可靠性和灵活性。
·程序模块化:程序由不同子模块构成,各子模块独立完成各自功能,互不干扰,因而程序结构清晰,便于修改。
·定时器的使用:程序中,利用不同的定时器来设定不同设备的延时时间,可以灵活地根据控制要求进行延时时间的设定。
2.5
部分程序梯形图
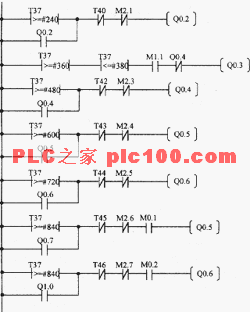
图3
部分联锁起停控制梯形图
图3所示为部分联锁启停控制梯形图,T37用于控制设备的启动延时,T40~T46用于控制相应设备的停车延时,接收到停车信号时,经过相应的延时,对应定时器置位从而实现联锁停车。Q0.3是1#破碎机的启动控制输出通道,启动1#破碎机时送出一个宽度为2s的正脉冲。Q0.7、Q1.0分别是2#给煤机、3#给煤机的控制输出通道,M0.1、M0.2
是内部标志位,用于保证2#、3#给煤机始终为一台工作,一台备用。
总之,本系统中,PLC作为现场控制设备,能够可靠、准确地完成控制操作,并且可以通过与上级工控机通信,组成分布式系统共同完成输煤系统的监测、控制要求,是现代工业控制中比较先进的控制方案,应用前景广泛。
目前,本系统已经在内蒙古伊化集团苏尼特碱矿电厂投入运行,能够可靠、准确地完成控制操作,实时监测和记录输煤过程运行状况,并且能对现场出现的各种突发事件及时做出响应,取得了良好的效果。